|
|
Read on web | Share this letter with a friend or a colleague
|
|
|
Why should you care about fatigue strength?
If a steel component in your car breaks, causing delay and frustration, metal fatigue is the most likely cause. If a wind turbine’s gearbox fails it will probably be for the same reason. Some references state that fatigue causes more than 90% of all mechanical failures. Therefore, by ensuring that critical components have a satisfactory fatigue performance, we can have a positive impact on the life cycle of mechanical structures and systems, resulting in more sustainable solutions.
Material selection plays an important role in determining fatigue life. In steel, the fatigue properties are primarily controlled by the material strength and the presence of non-metallic inclusions. For soft steels, the fatigue properties have a strong correlation with the matrix strength level. However, for high-strength steel, fatigue initiated by inclusions is dominant. Consequently, to improve the fatigue performance we need to both increase the strength and reduce the number of critically sized non-metallic inclusions. A large inclusion will reduce the fatigue life more than a small inclusion. Therefore, we should focus on minimize the larger features. So, what do we regard as a “large” inclusion? Well, we aim to control and limit inclusions with a size of 20µm or larger. This is because we know from our test programs that it is this size range that will cause fatigue failure in high-strength steels.
|
|
Finding the Needle in the Haystack
The most commonly-used standard method to determine the cleanness of a steel was developed many decades ago when steel quality was significantly lower. The number of large inclusions were much more frequent, and it was sufficient to investigate a relatively small
|
|
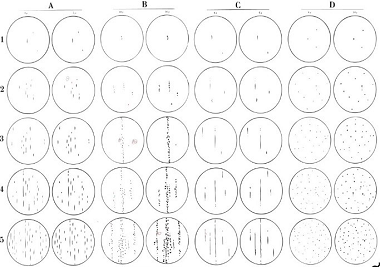 |
The JK chart was developed around 1930. The chart has been modified by introducing “half steps”, but the rating procedure has more or less remained the same.
|
|
sample to get a useful representation of the steel quality. This procedure, to polish a sample and study a small area in a light optical microscope (LOM), has remained the standard procedure. The actual area studied is about the size of a fingernail and normally a maximum of six samples are investigated.
Today, steel cleanness has significantly improved. The number of critically sized non-metallic inclusions are so scarce that that the
|
|
old methods fail to give a representative description of the steel quality. The probability of finding critically sized inclusions, even in standard quality steel, are so low that we lack data for descriptive statistics. The consequence is that it is not possible to predict if the fatigue limit of your high-strength steel component will be 400 MPa or 900 MPa, simply because the quantification method can not capture the right information.
|
|
New improved quantification techniques
If we can predict fatigue properties with a higher certainty then it becomes possible to increase the reliability of a component. It can also make downsizing possible since dimensioning, including safety margins, can be based on more accurate numbers. For vehicle components there might even be the possibility to reduce weight and increase the power density at the same time. This would give us a more sustainable solution.
In order to predict the occurrence of inclusion-initiated fatigue failures we need to know the number and size of defects present in the steel. At Ovako we call this “the true inclusion distribution”. If we have this data and know how the component is loaded with respect to the stressed volume and orientation, it is straightforward to estimate the fatigue properties. There is no secret in how to achieve this. We simply need to assess more material than we have previously. Preferably we should even assess material volumes instead of large areas. The reason is that to detect larger inclusions, you need to investigate a large volume. For smaller inclusions that have a higher frequency of occurrence it is possible to get enough statistics from a relatively small volume.
|
|
Ultrasonic scans using 25MHz showing 50µm defects
This is the reason why Ovako is using several techniques and merging theme together to get the true inclusion distribution. For the smallest part of the population we can rely on light optical or scanning electron microscopy of large areas. This gives us the statistical preferences of inclusions up to around 20µm. Above this size we use high frequency ultrasonic (>50MHz). This method makes it possible to detect inclusions in the size range 20-50µm in the material volume. However, this material volume is not enough to capture larger inclusions. This is the reason why we also perform a 25MHz ultrasonic testing since it covers a substantial volume and reveal defects over around 50µm. Finally, we use 10 MHz ultrasonic testing to account for the largest part of the population.
These tests come together to build a complete picture of the steel cleanness. Currently, we are using these tests on a daily basis to improve our products and processes. Some of our customers are also actively working in this field. In the future we will probably see these methods adopted as internationally recognized standard techniques. Ovako’s 10 MHz testing is already offered to our customers as a testing procedure. It is also available for everyone to use and possible to download from Ovako’s website.
|
|
|
Thank you for subscribing to Strength of Steel. Please invite any of your colleagues to join us and we look forward to continuing to bring you news of interesting aspects of the steel business we are all in together. Please remember to send us any questions you may have and we will do our best to address them in upcoming newsletters.
All the best,
Patrik Ölund, Head of Group R&D
|
|
Digital events 2022
Machinability and carbon neutrality. These are the subjects for our upcoming webinar program in the first quarter of the year.
In our webinar on February 9, 15:00-16:00 CET, Katarina
|
|
Kangert, Head of Sustainability and Safety and Göran Nyström, Group Marketing and Technology, will talk about our Carbon Neutral Now initiative.
We moved our first webinar of the year Machining guidelines for Ovako Steel products to a new date. How Ovako's new machining guidelines can help optimize your set up for machining operations. February 17 2022,15:00-16:00 CET,
Please click below to register.
|
|
|
Ask a question
Let us know what topics interest you and any questions you may have. We will do our best to answer them.
|
|
|
Join our community
If you are not already a member of the Strength of Steel community, please register by using the link below.
|
|
|
|
Strength of Steel landing page
After having published Strength of Steel newsletters for the best part of a year now we feel it is time to make them all available in one place.
|
|
|
|
This letter has been sent to | If you no longer wish to receive emails from Ovako, please unsubscribe | ©2022 Ovako, All rights reserved
|
|
|
|
Kungsträdgårdsgatan 10, 111 47 Stockholm, Sweden
Unsubscribe
|