|
Machinability matters
Welcome to the fifth monthly letter in our ‘Strength of Steel’ series. This time we focus on machining, something which is a key consideration for almost all of our customers. To ensure the best possible understanding of the interaction between tool and steel, we collaborate with leaders in machining. One such leader is Sandvik Coromant with whom we share many important development activities. Together, we are helping to optimize machining parameters for different executions of the same basic steel composition: Ultra clean versions, conventional versions and our proprietary M-Steel® treated version.
|
|
|
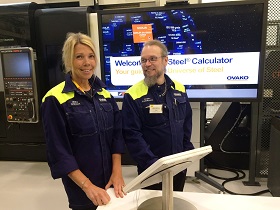 |
Ovako at Sandvik Coromant Tech Days
|
|
|
Recently we completed a Technical Report titled “Machining and tooling solutions for ultra clean steel for carburizing applications – turning”. You can find this report by using the link below. We believe the findings help to provide useful machining solutions when selecting a steel optimized for the highest fatigue strength. In powertrain applications this is therefore a key to achieving higher power density by using an ultra-clean steel.
|
|
|
|
|
A powerful illustration of the M-Steel effect
Earlier this year we completed a test that compared turning of M-Steel and conventional steel. The work was carried out together with Mitsubishi Materials experts at their Technology Center in Mooresville, NC, USA. We tested SAE 8620 (EN 20NiCrMo2-2) case-hardening steel in the as-rolled condition (200HB hardness), as well as SAE 4140 (EN 42CrMo4) quenching and tempering steel in +QT-condition (300HB). We machined the steels with rather severe machine settings which revealed an astonishing difference. For all the tests, M-Steel had a much longer tool life than the conventional steel. The major tool life criteria was flank wear. The protective deposit generated on the cutting tool by the M-Steel treatment really helped to reduce the heat transfer, enabling turning at high productivity. You can see examples of the comparisons below.
|
|
|
|
Grinding tests reveal further M-Steel benefits
Grinding is an important final step to achieve the close tolerances required for finished components and often involves extended cycle times that makes it an important cost consideration. Tyrolit Group is a global leader in this area so we collaborated with them to carry out tests at their Grinding Technology Department in Schwaz, Austria. Sharing common customers for powertrain components, we decided to carry out a grindability check on soft and hard versions of M-Steel, compared to corresponding conventional steels. Different discs and surfaces were subjected to a range of test conditions. We then evaluated radial wear, power consumption and surface roughness. The test engineers found that the wear of the CBN grinding wheel was almost halved with M-Steel, for both hard and soft grinding (relative G-ratio describing the grindability in the picture below). This is actually quite similar to our results from the hard part turning of carburized M-Steel using CBN cutting tools, where the rake face ‘crater wear’ of the CBN tools wass reduced by some 80%. Again, this is the result of the formation of protective layers from the M-Steel inclusions – the key to higher productivity.
|
|
|
|
With these three important collaborations, together with a long series of customer tests, we have built an important library of test results that can help us to improve the productivity for customers and end-users. My work in this area is fascinating and every week offers new angles to appreciate how machinability truly matters and can have a large impact on the cost efficiency of operations.
In our next Strength of Steel newsletter, we will move on to other topics and we would be happy to receive your suggestions or questions. Please stay with us as a subscriber and invite any of your colleagues that may also be interested.
All the best,
Thomas Björk
Group Technical Specialist, Machining
Ovako
|
|
|
Ask a question
Let us know what topics interest you and any questions you may have. We will do our best to answer them.
|
|
|
|
Join our community
If you are not already a member of the Strength of Steel community, please register by using the link below.
|
|
|
This letter has been sent to | If you no longer wish to receive emails please unsubscribe | ©2020 Ovako, All rights reserved
|
|
|
|
Kungsträdgårdsgatan 10, 111 47 Stockholm, Sweden
Unsubscribe
|